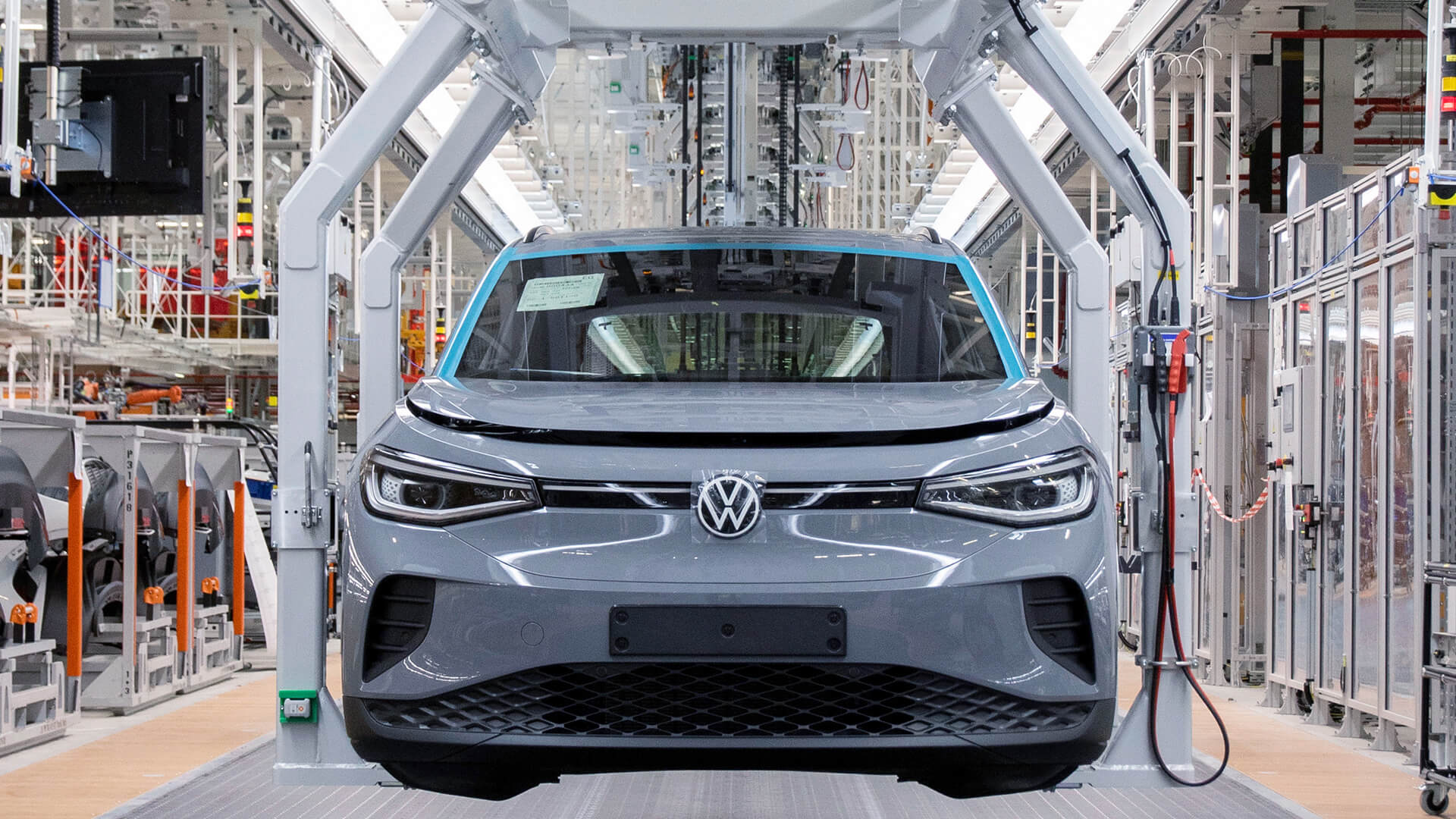
E-transformatieproces
bij Volkswagen in Emden
Het bedrijf bouwt zijn fabriek om tot een van de modernste fabrieken in de auto-industrie en een vuurtorenproject voor elektromobiliteit terwijl de productie doorgaat.
Volkswagen in Emden is de grootste industriële werkgever ten westen van Bremen en ten noorden van het Ruhrgebied. Op een oppervlakte van 4,3 miljoen vierkante meter worden ongeveer 163.000 voertuigen per jaar geproduceerd, waaronder de Passat, Arteon en ID.4 modellen en, sinds 2023, de vierdeurs volledig elektrische Volkswagen Aero. De productie van de Passat en Arteon modellen met verbrandingsmotor wordt nog tot uiterlijk 2024 voortgezet, waarna wordt Emden een zuiver elektrische fabriek.
Sinds november 2018 bereidt de locatie aan de Noordzeekust zich voor op het grootste transformatieproces in de geschiedenis van de fabriek: Volkswagen investeert ongeveer een miljard euro en bouwt de fabriek om tot een van de modernste fabrieken in de auto-industrie en een vuurtorenproject voor elektromobiliteit terwijl de productie doorloopt. Sinds 2020 werd onder meer een nieuwe carrosseriehal, een tweekleurenhal en een nieuwe montagehal gebouwd. Het concern richt zich daarbij op milieuvriendelijke en grondstofbesparende technologieën.
Automatische slice picking voor “just-in-sequence” in plaats van “just-in-time”
Dit geldt ook voor de productie van de ID.4. Dit is waar onze nieuwste technologie voor automatische slice picking bij komt kijken. De taak van de eerste constructie van dit type is om ruiten van verschillende vormen en kleuren in een ladingdrager te plaatsen in de exacte volgorde waarin de overeenkomstige voertuigen de productielijn verlaten, d.w.z. een “just-in-sequence” levering in plaats van een “just-in-time” levering. Wat voorheen moeizaam met de hand en met een onvoorspelbaar foutenpercentage moest worden gedaan, wordt nu nauwkeurig en betrouwbaar gedaan door een speciaal geprogrammeerde robot met behulp van railtechnologie.
Digitale simulatie tot op de centimeter nauwkeurig
Het gebruik ervan bespaart niet alleen hulpbronnen, maar ook aanzienlijk tijd en moeite tijdens de planning en installatie. “Het scenario werd vooraf tot op de centimeter nauwkeurig digitaal gesimuleerd om de structuur in de krap berekende ruimte tussen de bestaande VW-installatietechniek te kunnen plaatsen,” zegt Daniel Springfeld, onze verantwoordelijke projectmanager in de vestiging van Bremen. “Dit was zowel voor ons als voor de klant een primeur. Het enige dat ter plekke nodig was, was het afstemmen van de robotprogrammering, zodat de productie binnen zeer korte tijd van start kon gaan.”

Opbouw en montage in de hal van VW
Nog een pluspunt voor het besparen van hulpbronnen is het gebruik van zo identiek mogelijke onderdelen voor de opbouw van de slice picking en de montage van de ruiten in de voertuigen. Dit betekent dat individuele onderdelen in de toekomst ook kunnen worden gerecycled, gunstig kunnen worden ingekocht of als multifunctionele reserveonderdelen kunnen worden gebruikt.
Uitdagingen aangaan met ongebruikelijke ideeën
Dat het hele project op tijd kon worden afgerond ondanks de knelpunten in de leveringen tijdens de Corona-pandemie, was niet in de laatste plaats te danken aan een vindingrijk idee van Robert Straub, afdelingshoofd in Bremen. “Tijdens het testproces van het systeem was er een gebrek aan veiligheidsautomaten, die gewoonweg niet beschikbaar waren. Maar zonder veiligheidsautomaten is er geen elektriciteit. Daar de technologie van deze automaten tot op de dag van vandaag niet echt is veranderd, heb ik gewoon die van mijn modelspoorbaan geïnstalleerd. Zo konden we ons ondanks de leveringsproblemen aan de planning houden en het systeem op tijd leveren.” Soms moet men gewoon onconventionele paden bewandelen om een oplossing te vinden. Ook VW projectmanager Holger Raschke leek zichtbaar onder de indruk van de creativiteit van onze collega’s. “Menig idee dat ons in het begin bijna absurd leek, bleek uiteindelijk de enige mogelijke en bovendien zeer efficiënte oplossing te zijn,” voegt hij enthousiast toe. “Men kan de ervaring gewoon voelen. Ondanks alle uitdagingen maakt dit samenwerken natuurlijk leuk.”